The
process involves two steps:
Chemical Stripping
E-Coating
Chemical Stripping:
Old steel must first be cleaned of rust, paint, filler and
other dirt and contaminants. The stripping process starts by baking
the part for 8 hours at 800°F. Warping does not occur because
the temperature changes are very gradual. Following baking,
the part is submerged in a hydrochloric acid solution. This
removes any remaining residue. Next, the part takes a quick
dip in a neutralizer bath to wash off the acid solution. The
cleaned, chemically stripped piece is then coated with a water
soluble oil to inhibit any surface corrosion until the part is
e-coated.
E-Coating:
Following chemical stripping, the part proceeds into a wash to
remove the water soluble oil and prepare the part for coating.
After washing, the part is immersed in zinc-phosphate which is
a rust inhibitor. The part is then dipped in a vat of PPG
epoxy primer, which is electrostatically applied. The
electrocoat bath consists of 80-90% deionized water and 10-20%
primer solids. The deionized water is the carrier for the
primer solids. The primer solids consist of resin and pigment.
Resin in the primer provides corrosion protection,
durability and toughness. Pigment in the primer provides color
and gloss. During the electrostatic dip process, the
thickness of the primer on the part is regulated by the amount
of voltage applied to the part. Once the coating reaches the
desired film thickness, the part will no longer conduct the
electrical charge and the accumulation of the primer on the
part is completed.
After leaving
the coating vats, the part is sent to the bake oven. The bake
schedule is about 45-60 minutes (or until well done), with
part temperatures at approximately 375° F.
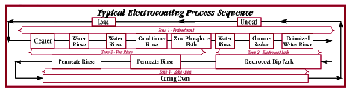
Click on the image for an enlarged
version. |